鋼鉄材料の厚物加工
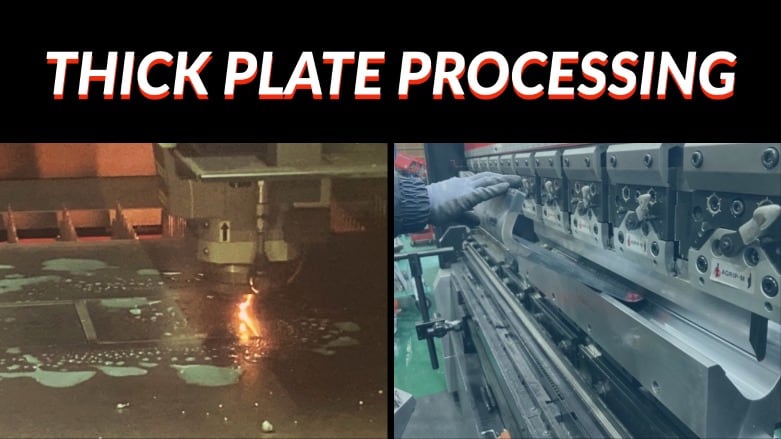
先日、ファイバーレーザ加工機に、新たな条件設定を追加しました。(正確に言うとメーカーのAMADAさんがやって下さった訳ですが...)。
新製品開発の為に、現在まで研電社では扱っていなかった厚物の鋼材の加工が必要になったからです。一般的に、板が厚くなると加工の難易度は上がります。
今回は、レーザ加工機とプレスブレーキで初の厚物加工に挑戦した様子をお伝えします。金属加工特有の用語が随所で出てきますが、是非最後までお付き合い下さい。
レーザ加工
SS400 (よく使われている比較的安価な一般構造用鋼材) の板厚3種、16mm・22mm・25mmの酸素切断を試行しました。 すると、品質を悪化させる要因の一つであるセルフバーニング(過剰燃焼)が発生しました。この「セルフバーニング」は、母材の鉄とアシストガス(酸素)が過剰に反応し、レーザ光の照射部外まで切溝が広がってしまう現象で、厚物加工でしばしば起こります。
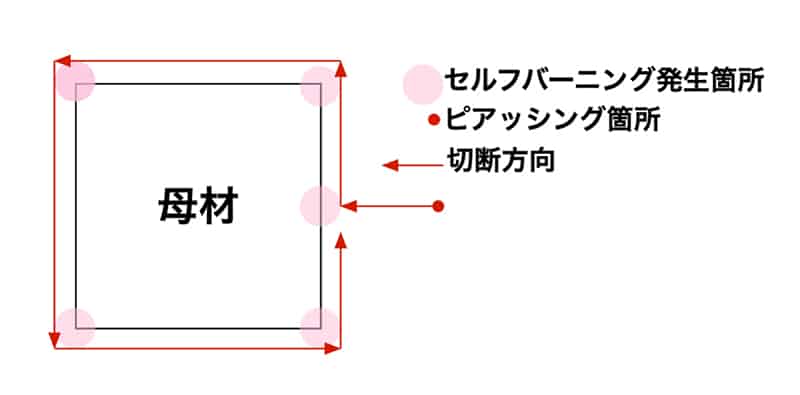
これに対して、以下3項目の対策を行いました。
- 冷却水による母材の冷却
弊社のファイバーレーザ加工機には母材へ冷却水を吐出する機構が備わっています。 - 加工条件の変更
レーザ加工の途中で加工しない期間(レーザ光による温度上昇が無い期間)を節々に設けて断続的に加工する事で母材の温度上昇を低減させました。ただ、この方法では一工程にかかる時間が長くなりますので、今後QCD(品質・コスト・納期/製造スピード)のバランスを見極め、最適解を模索していく必要があります。 - 加工手順の変更
ピアッシング箇所(最初に穴を開ける場所)と切断方向を変更しました。
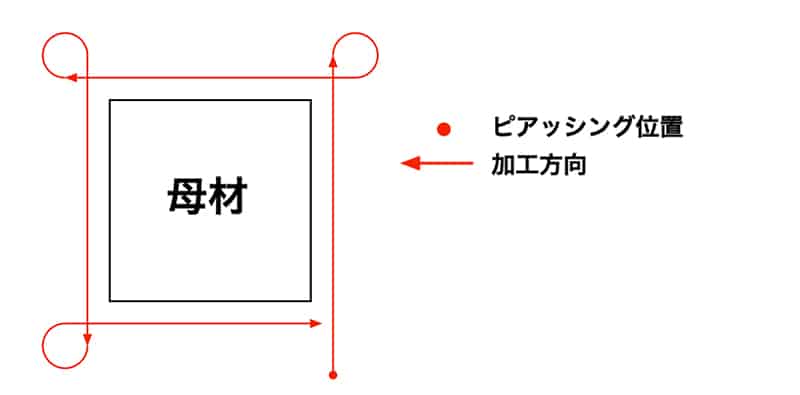
これでセルフバーニングは解消されましたが、他に厚物のレーザ加工に起こりやすい問題として、切断面のテーパー形状(ベベル角)が顕著になりやすい事もあげられます。
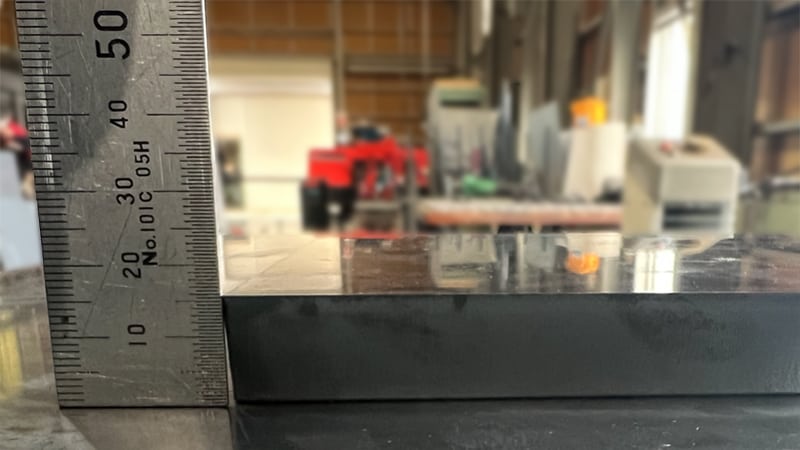
ファイバーレーザー切断はベベル角が小さいことが特徴ではあるものの、今回は1-1.5度の角度がついていました。
設計担当者は留意が必要ですね。
条件の精緻な設定は今後の課題ですが、結果として、ドロス(レーザ加工の際、裏面に付着する玉状や氷柱状の溶解金属)や切断面のダレも少ないように思えました。
曲げ加工
先ほどレーザ加工機で切断したSS400、厚さ16mmの板に、サーボプレス機でV曲げ加工(V字の型に押し込んで曲げる方法)を施します。幅125mmのV型は、全長にすると重量がかなりありますので人力ではセットできません。その為、短く分割したものを並べて使用しますが、この分割された型も1つで41kgあります。
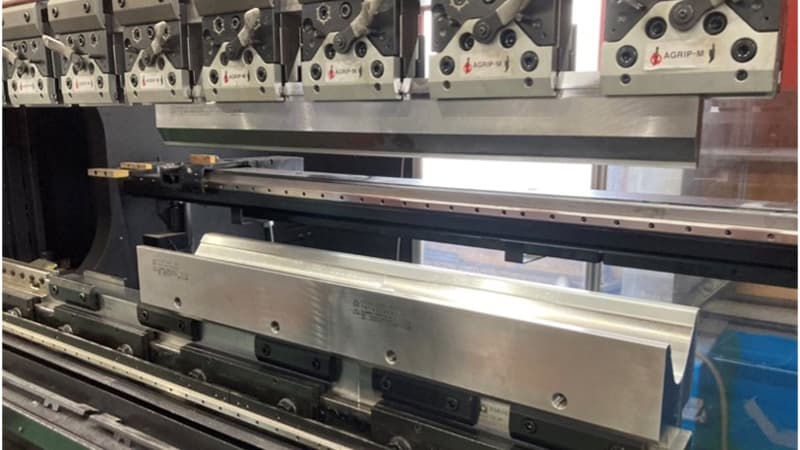
鉄板の幅270mmに対して荷重を1322kNかけ、塑性変形時に発生する伸び値・スプリングバック値(上型を上昇させ圧力をなくした時に母材が元の形状に戻ろうとする弾性回復)などを測定しました。
この伸び値をCAM上にて補正・条件設定することで、熟練技術によくある暗黙知の形式知化を図ることができるでしょう。
また、厚物の曲げ加工は、加工の端面に生じる「曲げコブ」が大きくなります。この曲げコブは、後の工程に影響を与える場合があり、通常はサンダー処理などで削り落とすことになります。しかしながら、レーザカット時に曲げコブ量を補正したくびれのような形状に切断することで、サンダー処理等の工程を削減できます。
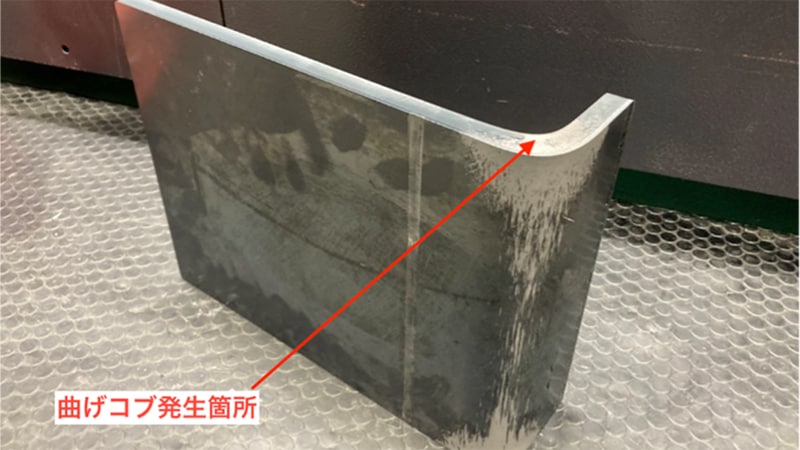
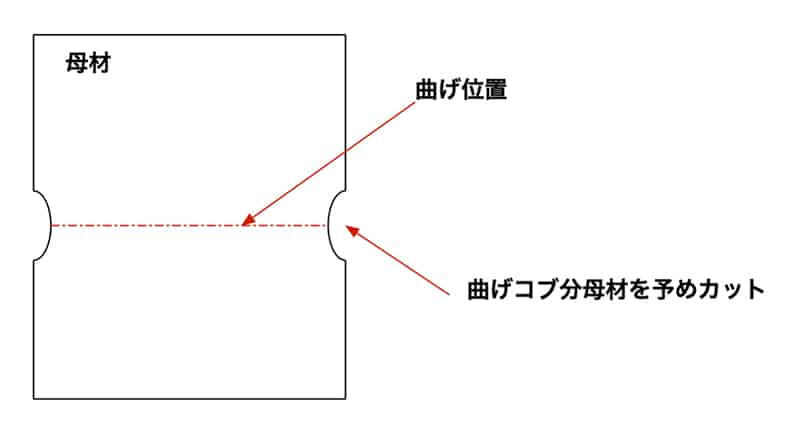
新製品の完成度を高める為、今後も研究を続け、最適な加工方法を模索していきます。